
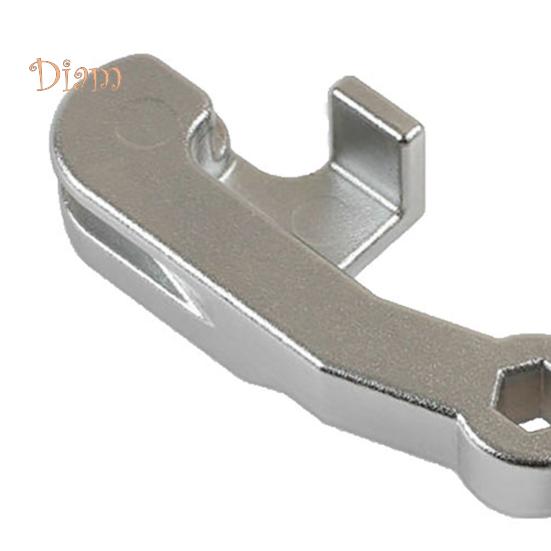
The percentage boost is the primary controllable factor affecting the wall thickness and strain of a tube due to bending, hence its usefulness. The level of boost controls the movement of the back of the tube feeding into the bend, which affects the thickness and strains generated in the tube during bending. This ratio is then converted into a percentage and this is called "percent boost".
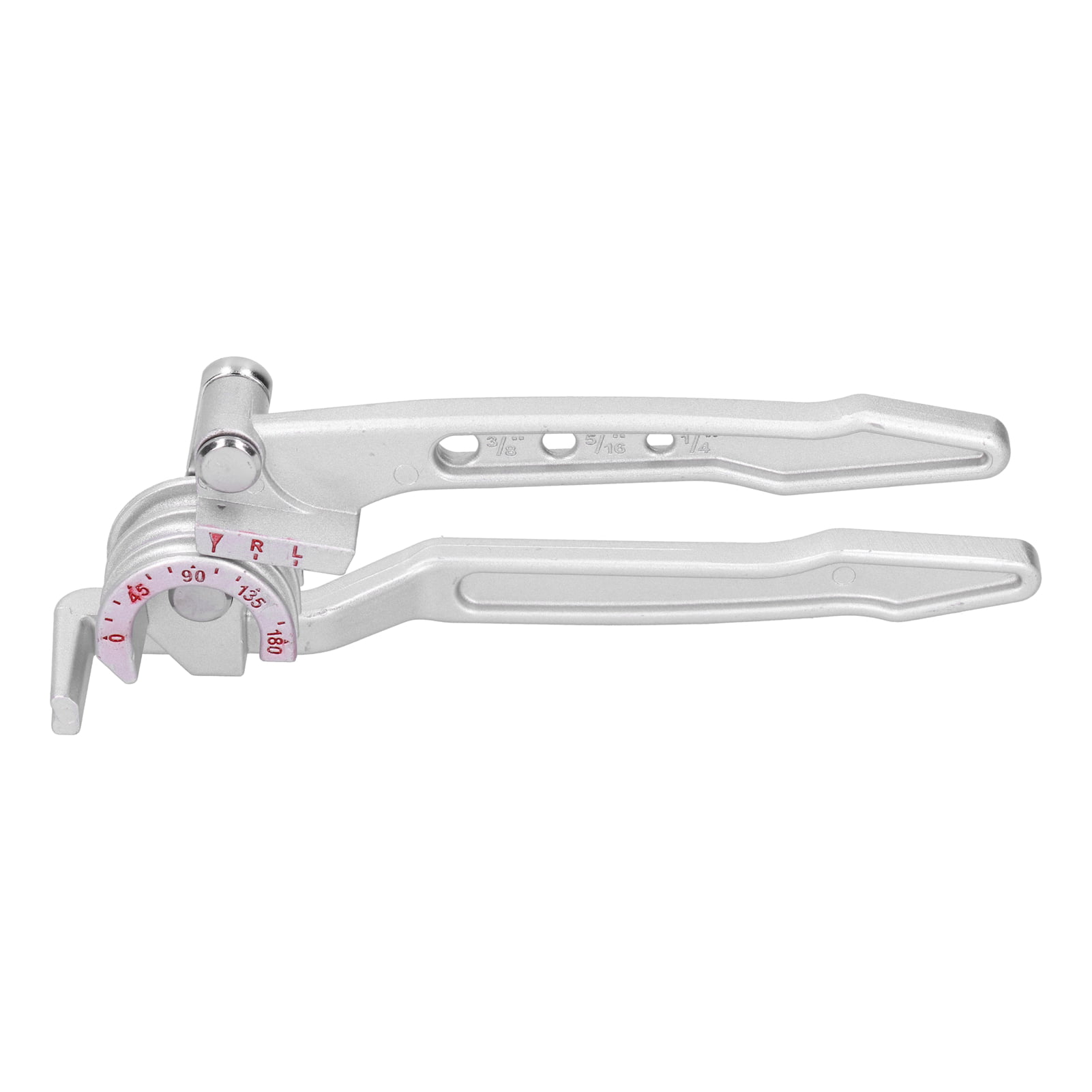
The tangential velocity of the bend die, at radius R c, is equal to R c w, during the bend, where w is the angular velocity of the bend die as it rotates. The percentage boost is the ratio of the instantaneous linear velocity of the pressure die ( V pd), to the instantaneous tangential velocity of the rotating bend die, at tube centerline radius R c. It "forces" material into or out of the bend as a way to control the wall thickness and strains imparted onto the tube during bending. The percentage boost is also called an axial assist. The mandrel helps to prevent wrinkles and ovalization of the tube during bending. First, it must exert sufficient clamping pressure by pushing the tube against the wiper die (inclined at a small rake angle) to prevent wrinkling on the inside bend of the tube, and secondly it must control the axial movement of the back of the tube feeding into the bend. The role of the pressure die is two-fold. To control the axial tube motion, the pressure die applies axial force to the tube either through friction (between pressure die and tube) or through an optional boost block (as shown), which pushes against the back of the tube during bending. The rotation is continued until a desired tube bend angle is reached. With the tube in place, the bend die and clamp die then rotate around as one piece, bending the tube around the bend die, with the pressure die maintaining pressure against the wiper, and moving along in the axial direction at a prescribed percent boost. It is then locked in place by closing of the clamp die onto the bend die. To bend a tube in a rotary-draw bender, it is first positioned inside the bender. The figure below illustrates a rotary draw tube bending process along with the names of the tooling used.
#ACCURATE TUBE BENDING TRIAL#
Having the means to predict tube geometry after bending is useful as a manufacturing aid since it can reduce trial and error during prototyping. The computer model also estimates the force and torque required to bend tubes to a given radius. I also studied the physics of bending tubes and developed a computer program to predict the stresses, strains, wall thickness, and springback of a tube after bending. For my Master's degree project I researched rotary draw tube bending which is a common method used to bend tubes. Tube bending is a general term used to describe the metal forming process used to permanently form tube or pipe.
